Technologies
Capabilities
contributors
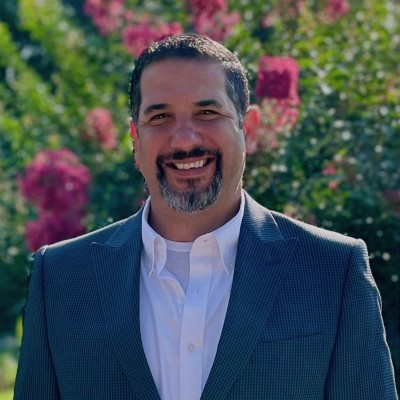
Robert Olszak
Vice President, Manufacturing & Logistics
share article
Supply chains are still feeling the impact of pandemic-driven rising costs and delays. Digital solutions such as predictive analytics, blockchain and digital freight matching may address some of today’s challenges, but long-term success lies with stronger alliances and better coordination.
Although no one can accurately predict the future, recent events have certainly elevated the discussion about the future of logistics in America. Not only did the lessons of 2020 provide a foundation for redesigning logistical networks, additional data with enhanced AI capabilities are now providing industry leaders with more intelligent—and actionable—data points to shape their logistics and transportation strategies.
Digital supply networks and the use of predictive analytics to forecast demand top the list of emerging trends shaping the supply chain landscape, along with equally important trends such as:
- Blockchain-related solutions that provide materials and product real-time visibility for complete product lifecycle management
- Increases in driver wages, with some companies offering significant sign-on bonuses to close the gap on driver shortages
- Digital freight matching with higher dependencies on smaller regional carriers and contracted freight forwarders
- Higher demand for cold chain solutions for transporting temperature-sensitive goods such as pharmaceuticals
- Businesses departing from traditional manual methods for managing materials movement, freight schedules, and driver management
E-commerce was already on a trajectory for rapid growth before the pandemic, but with stay-at-home quarantines impacting millions, more people than ever turned to online shopping for almost everything, including medications, clothes, household goods—even groceries. This surge in demand posed additional constraints on final-mile delivery. With longer lead times, materials shortages, manufacturing delays, and asset restrictions, the American public can expect even greater delays moving forward. Although many of us have become accustomed to same-day delivery or expedited shipments at a lower cost, this will inevitably change.
Consumers: Watch for Rising Costs
The rising cost of crude oil and fuel will also continue to drive rising freight costs. Factor in significant capital investments by organizations in digital and infrastructure transformation, and consumers can expect some of this cost burden to be passed on to them in higher shipping costs. To offset transportation expenses, expect logistics companies and third-party logistics providers holding shipments to maximize freight capacity—or consolidating goods to central distribution points—to save costs where they can. Once again, the consumer has to expect further delays and disruptions to delivery times.
Infrastructure Legislation: Needed, but Expect Impacts
Another point of interest is President Biden’s proposed infrastructure bill. Should it pass, a sensitive domestic transportation network will likely face an increased surge in freight demand, coupled with long-term infrastructure delays, with drivers’ hours of service potentially negatively impacted due to transportation infrastructure overhauls.
Additionally, expected tax increases could hurt US manufacturers and potentially compromise the economic recovery. This is especially true in a sector where there’s a growing dependence on domestic manufacturing growth and near-shoring alternatives. At any rate, expect a ripple effect that could add more challenges to logistics and transportation nodes.
Construction: Expect Delays
Materials shortages continue to plague public communication, as the narrative evolves around the future of supply chains. For many of the reasons cited above, consumers, small businesses, and contractors—especially within the construction industry—face a tipping point. If it’s taking longer to receive critical materials such as steel rebar and lumber, what’s the cost impact for the final delivery of goods when faced with work stoppages, shutdowns, and additional delays?
Let us assume that lumber, for example, arrives at a job site two weeks after the expected delivery date, with some of the material compromised and no longer usable due to extended exposure to the elements. Waste is created. The cost will go up. Projects will take much longer to complete than budgeted. These types of overruns will inevitably have a downstream impact on logistics cost and total value performance.
The same can be said for grocery stores, as they are forced to reshelve products with limited safety stock. American consumers should expect more empty spaces on grocery store shelves in the months ahead—with everyone struggling to solve a looming problem with many influential elements beyond their control.
Inventory: Optimization Is Key
You can’t have a thorough conversation about the future state of domestic transportation and logistics without commenting on inventory. More companies seeking short-term alternative solutions are shifting their attention to inventory segmentation. Unable to redesign their distribution network overnight, product placement becomes critical. In essence, it’s all about shortening the distance from the point of distribution to the end consumer.
As a result, there’s increased demand for inventory optimization solutions, such as SKU rationalization or product rationalization. With raw materials constraints, which finished goods products should be manufactured to meet demand? What are the carrying stock levels for the selected products? In contrast, what products and materials have a lower velocity, even creating obsolescence? Balancing operating overhead with revenue growth is sometimes a question of working capital allocation.
Moving upstream, there’s now a laser-like focus on materials procurement and re-evaluating the triggers for demand and replenishment. With longer lead times and forecasting limitations, it’s a balancing act to procure critical materials, components and goods to sustain a healthy supply chain of in-demand products. In response, logistics providers seem to always be anticipating the next big surge in demand with major blind spots.
Needed: Stronger Alliances and Better Collaboration
All of this points to the need for better collaboration and cooperative strategic alliances among suppliers, manufacturers, companies, logistics providers, and customers. Without transparency among these players and the use of digital technology-enabling tools, many companies will continue fighting a losing battle. Those who can perfect these interdependent relationships across the supply chain will reap the benefit of increased market share. Those that can’t—including those making no changes at all—will fall further behind.
Adding to the many existing challenges on the table, there’s yet another level of uncertainty to add to the mix: the upcoming hurricane season as well as severe drought conditions in the western US, which could lead to another record fire season ahead. Companies that responded well to the pandemic may be better able to deal with either challenge from nature, but that remains to be seen.
None of us have a crystal ball that can predict the future. However, there are tools available that can enable enhanced planning and execution, mitigating risks that ultimately impact cost and total performance. Logistics companies, suppliers, manufacturers, and consumer-based organizations would benefit by developing strategic coalitions to tackle the near-term and long-term challenges. Rather than working independently from one another, or even as competitors, we need to harness shared technologies, data, and intellectual property to create more sustainable solutions.
If the pandemic taught us one thing, it’s that we’re all in this together. In that same spirit, we’ll need to work together to solve supply chain challenges as well.